QC Story – Testing and Verification of Theories
by: Quest Claire
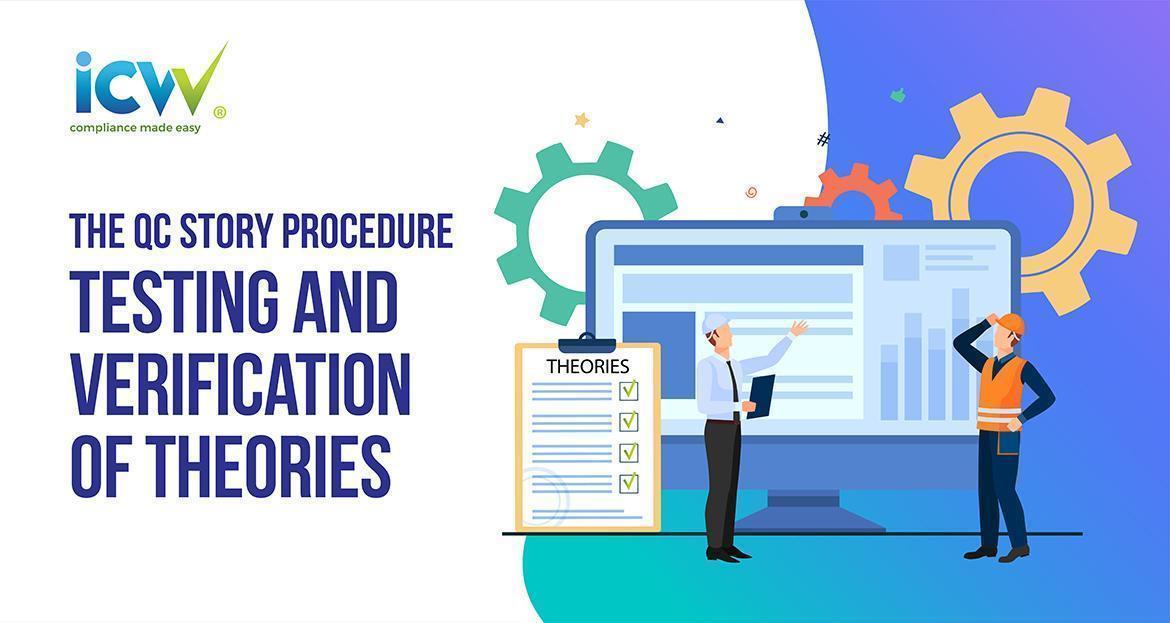
Now I come to the next phase of the QC Story Procedure.
Testing and verifying theories are important as they are easily susceptible to errors. When correctly done, subjective accusations of causes of problems become objective evidence, which opens the avenue for promising results.
In most projects, secure information beyond that available from past data is needed. Much of this missing information comes from the study of current production. There are multiple forms of such study; collectively, they are the most valuable set of tools for diagnosis. They include process capability studies, dissection of the process and product, discovering hidden contributing parameters, and providing special instruments to measure with greater precision than the conventional shop instruments.
I like to use the spray painting case study from the last toy factory to introduce the process of testing and verifying the theory. I want to use the previous table and chart (Table 1 and Chart 1) again to refresh our memories. These data were collected before any theories were established and any process improvement actions were taken.
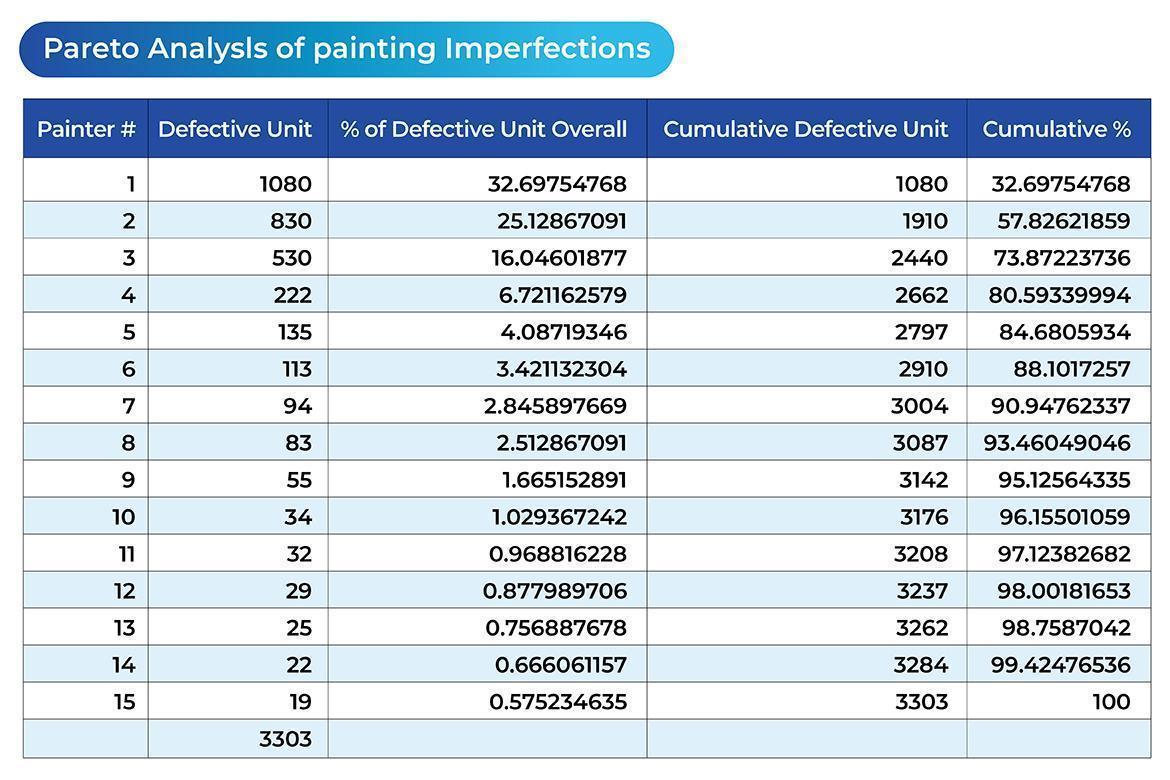
Table1
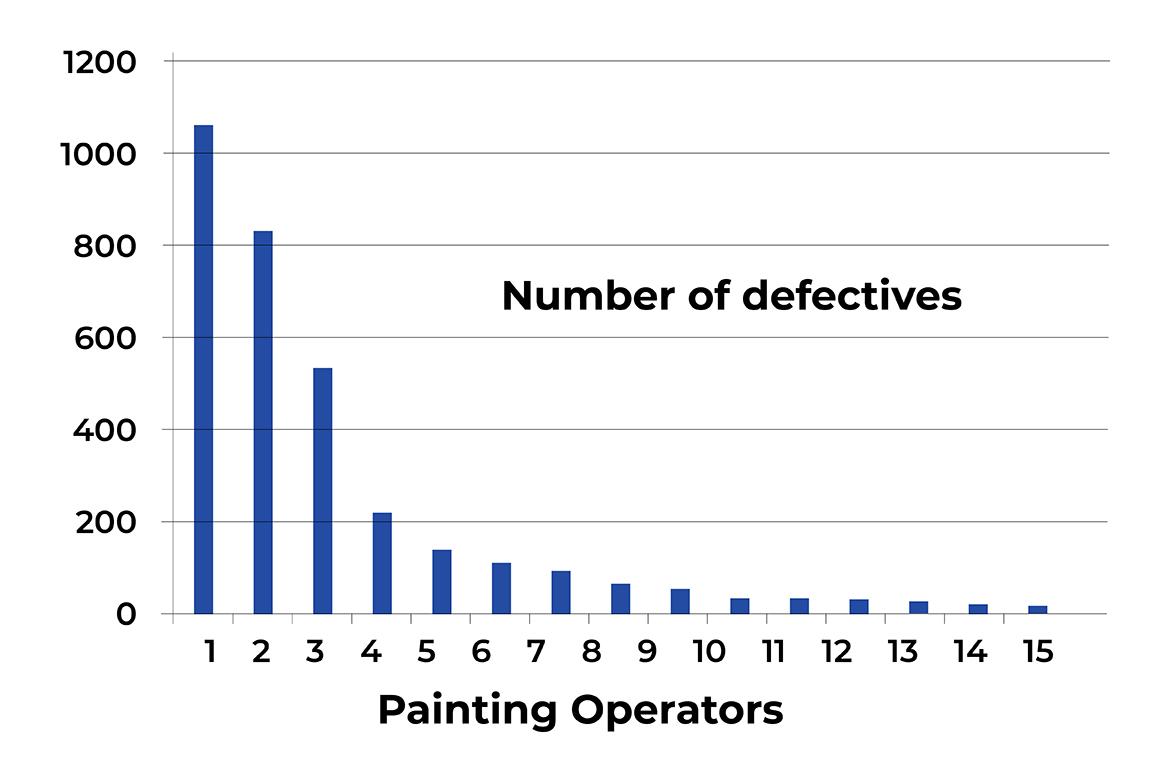
Chart1
To address the vital few problems, I like to focus on Painter #1, as he accounted for most of the defects, 32.7% of all the defects of the 15 painting operators.
Observation Summary (Referring to Tables 1 and Chart 1)
· Majority of the defect was from Painter #1.
· Painter #1 is comparatively new to the spray paint process despite basic operation training being provided, according to Production Manager.
· Painter #1 worked on the Doll Face Feature during the first 3 weeks (week 1, week 2, and week 3) and then worked on the Doll Hair during week 4.
· Production information and inspection data record are consistent with the change of spray-painting location during the 4 weeks.
· Paint Mask A is for Doll Face Feature, which covers painting on the eye, nose, lip, and ear; the spray paint goes through a narrow opening of the mask before reaching the doll face, while Paint Mask B is for Doll Hair, an open mask which shields the non-painted portion of the doll, for a hollow mask, the spray paint does not go through any narrow opening.
Firstly, we examined the total of 1080 defects he had produced during each of the 4 weeks, trying to determine if different times could cause a change in some defects produced. From the following charts, which were made based on the inspection data record from the production department, we could see a major reduction in defects in week 4 (see Chart 2). Therefore, we wanted to know if there was any process change in week 4.
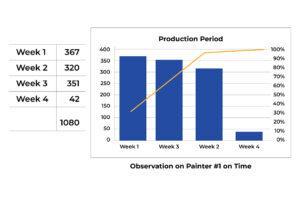
Chart2
Secondly, we reviewed the inspection data record and examined the defects spread over the painting locations. Painter #1 worked during these 4 weeks, determining if the painting location could cause a change in the number of defects produced. The following chart showed a major reduction in defects when Paint Mask B was used instead of Paint Mask A (see Chart 3). Therefore, we wanted to find out why there was a drop in defects from using a different spray mask.
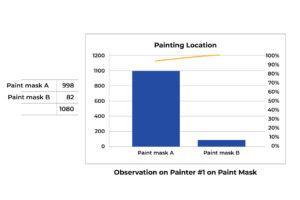
Chart3
Thirdly, we examined the 1080 defects he produced during these 4 weeks, trying to determine if different paint products could cause a change in some defects produced. From the following chart (Chart 4), which was made based on the inspection data record from the production department, we could see a major reduction of defects in painting the Doll Hair compared to the Doll Face Feature. Therefore, we wanted to find out why there was a drop in the number of defects from painting a different doll location using a different spray mask.
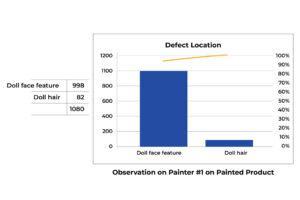
Chart4
Lastly, we examined the 1080 defects Painter #1 produced during these 4 weeks to determine if he had different painting defects and their corresponding frequency. From the following chart, which was again made based on the inspection data record from the production department, we could see a substantial reduction of defects on the “Uneven Paint” compared with the other defects (see Chart 5). From the inspection data record, I was advised by the QC manager that the “Uneven Paint” defect was only associated with the Doll Hair painting operation but not associated with the other Doll Face Feature painting operation.
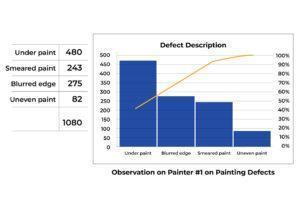
Chart5
Theory Established: work between the QC manager and spray-painting process engineers
· A spray-painting mask with a narrow opening must be cleaned with a chemical solvent every 10 sprays to prevent the excessive paint from staying next to the opening, causing blockage to the spraying operation. Failure to follow this cleaning process was confirmed to be the major assignable cause of the defects produced.
· Painter #1 was comparatively new to the job and needed to be instructed to enforce the chemical solvent cleaning in the initial training.
· Production information and inspection data record are consistent, pointing to the likelihood of validity of this single theory.
· Corrective actions for process improvement are to follow by referencing the theory established.
Three months after the process improvement actions were implemented, I had an opportunity to meet with the production manager and the toy factory’s QC manager again. Production information and inspection data record were retrieved, examined, and analyzed again to verify the extent of the process improvement. Similarly, inspection data records for 4 consecutive weeks were used, and we got the following process quality control inspection records as shown in the following tables (see Table 2 and Chart 6).
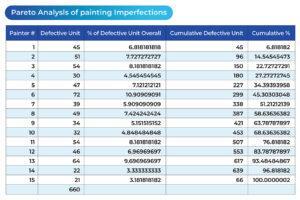
Table2
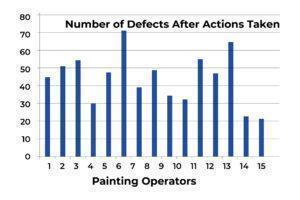
Chart6
Therefore, we all agreed to summarize all the corrective actions based on the theory established, based on the causes and effects pertinent to Painter #1 for producing the relatively high number of defects during those 4 weeks.
Actions implemented based on Theory Established
· Work instructions for each spray-painting location are provided and displayed conspicuously. Instructions are stated as “Spray mask is required to be cleaned by the supplied chemical solvent every 10 – 30 sprays to prevent the excessive paint from staying next to the opening, causing blockage to spraying operation.
· The operation supervisor should train all new painters to ensure the cleaning process is conducted correctly. The cleaning frequency is verified to be adequate for that specific opening, and paint viscosity ensures that the intended paint spraying is maintained.
· The operation supervisor reviews the inspection data record every day instead of the production manager every week.
· The production manager is to verify quality improvement every month.
As the theory is verified, the remedial process now begins. The process has yet to be verified to confirm its capability, which I will further touch on in the next article.