The QC Story Procedure
by: Quest Claire
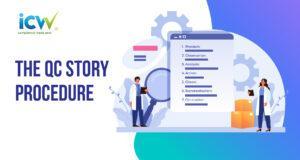
I understand the importance of the role of my supervisor, VP Merchandising, with a primary objective of putting merchandise on the retail floor and having products ready to be shipped from the warehouse when customers’ orders come. Any recommended process improvement actions must be clearly understood, backed by reasons, and supported by evidence. If there is a possibility that a process improvement action may delay or may add costs to the process, such an impact must be reviewed carefully with relevant quality cost analysis. Process improvement actions should only be taken when the company management sees an overall cost reduction. Otherwise, recommended actions will be recognised simply as imagination or desk theory and perceived as bad for the business.
People in the manufacturing industry often say quality is everybody’s business. A consumer product can easily contain dozens of parts and materials contributing to product quality. If any of them is located out of its tolerance for its intended use, the product will be defective. Unless a process improvement plan is clear and logical, getting management support for implementation won’t be easy. In other words, the management wants to understand how a program is implemented. The next question is what tool is available. To impress the management, I DO have a program that has been carefully designed, will be carried out step-by-step, will provide opportunities to verify its effectiveness during its rollout, and will complete with measurable goals. Therefore, I consider that the QC Story Procedure tool is the right one as it is easy to understand and use. I expect that the management would likely be convinced about the plan’s effectiveness and render necessary support. I believe the tool contains clear concepts and maintains a fluid flow of thoughts followed by logical conclusions. The QC Story Procedure tool is explained as follows:
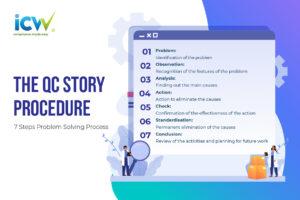
The QC Story Procedure
The QC Story Procedure is designed for problem-solving. A problem is defined in the QC Story as:
A problem is the undesirable result of a job.
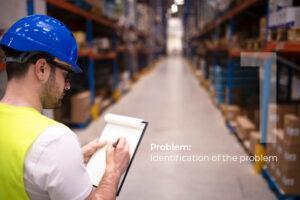
1 Problem
Activities
- Show that the problem being handled is of much greater importance than any other problems.
- Show what the background of the problem is and what its cause has been so far.
- Express in concrete terms only the undesirable results of poor performance. Demonstrate the performance loss in the present situation and how much it should be improved.
- Set up a theme and a target, and sub-themes if necessary.
- Nominate a person to take charge of the task officially. When a team carries out the study, nominate the members and the leader.
- Present an estimated budget for the improvement.
- Make a schedule for the improvement.
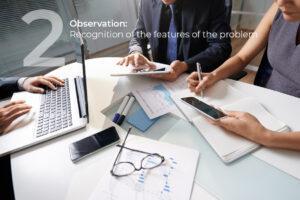
2 Observation
Investigate the specific features of the problem from a wide range of different viewpoints.
Activities
- Investigate four points (time, place, type, and symptom) to discover the features of the problem.
- Then investigate from many different points of view to discover the variation in the results.
- Go to the site and collect the necessary information that cannot be put into a data form.
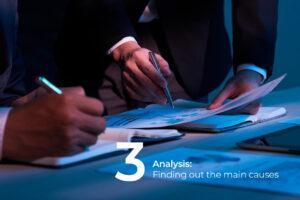
3 Analysis
Find out what the main causes are.
Activities
- Set up hypotheses (select major candidates as causes).
- Write down a cause-and-effect diagram (a diagram that contains all elements seemingly related to the problem) to collect all knowledge concerning possible causes.
- Use the information obtained in the observation step and delete any elements that are not relevant; revise the cause-and-effect diagram using the remaining elements.
- Mark those elements in the latter diagram which seem to have a high possibility of being the main causes.
- Test the hypotheses (derive the main causes from the candidates)
- From elements with a high possibility of being caused, devise a new plan to ascertain the effect those elements have on the problem by obtaining new data or carrying out experiments.
- Integrate all the information investigated and decide which are the main possible causes.
- If possible, intentionally reproduce the problem.
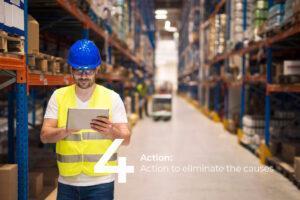
4 Action
Activities
- A strict distinction must be made between actions taken to cure phenomena (immediate remedy) and activities brought to eliminate cause factors (preventing recurrence).
- Ensure the actions do not produce other problems (side effects). If they do, adopt other measures or devise remedies for the side effects.
- Devise several different proposals for action, examine the advantage and disadvantages of each and select those to which the people involved agree.
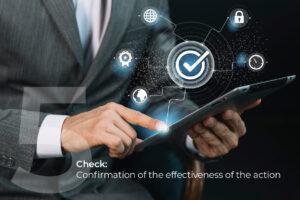
5 Check
Make sure the problem is prevented from occurring again.
Activities
- In the same format (tables, graphs, charts), compare the data obtained on the problem (undesirable results in the theme) before and after the action has been taken.
- Convert the effects into monetary terms and compare the result with the target value.
- If there are any other effects, good or bad, list them.
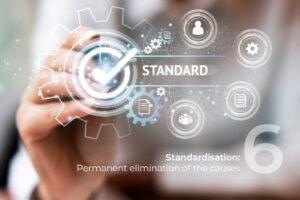
6 Standardization
Eliminate the cause of the problem permanently.
Activities
- The five Ws and one H: who, when, where, what, why and how, for the improved job must be identified and used as a standard.
- Necessary preparation and communication regarding the standards should be carried out correctly.
- Education and training should be implemented.
- A responsibility system must be set up to check whether the standards are being observed.

7 Conclusion
Review the problem-solving procedure and plan future work
Activities
- Sum up the problems remaining.
- Plan what is to be done to solve those problems.
- Think about what has gone well and badly in the improvement activities.