Pre-shipment Inspection – Lot Inspection & Sampling Plan
by: Quest Claire
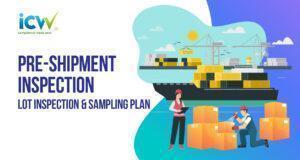
1. Lot formation
One day, an urgent order for a large quantity of product (30,000 pieces) was required to complete production within a short time.
The producer informed us that they had to split the output between their two production sites, which had previously been produced for us. Still, different manufacturing teams run their production separately using different assembly machines and production supervisors.
When the 30,000-piece order was ready for pre-shipment, the producer asked me if I wanted to conduct one single inspection for the entire lot (option 1) or two inspections per site of 15,000 pieces each (option 2). My quick calculation showed that option 2 costs twice compared to option 1. Therefore, I chose option 1 to save costs for the company without giving it a second thought.
The inspection results failed the acceptance criteria as the number of major defectives was found to be 20 from a sample of 315 pieces, exceeding the acceptance number of 14 under AQL 2.5%. Our policy requires the producer to conduct a 100% screening and present the lot for a second inspection. The producer reported that in their screening, they found 2% defective from the 30,000-piece lot and wanted a second inspection, which took place on the third day after the first inspection.
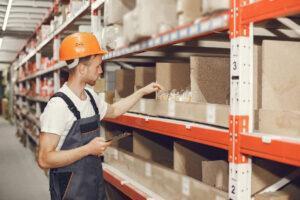
Surprisingly, the inspection results failed the acceptance criteria again as the number of major defectives was found to be 16 from a sample of 315 pieces, again exceeding the acceptance number of 14. This second failure was brought to the attention of my supervisor as this was an important order and on-time shipment is critical.
I then reviewed that situation with our contract inspection company immediately. They recommended treating each 15,000-piece lot from each site as a different product and inspecting each lot separately. I then instructed the producer to do that in the third inspection. The producer reported later that after the 100% screenings, they found from the two screenings a total of 1% major defectives from site A and 10% major defectives from site B.
Both lots also passed the third inspection, with inspection results of 4 defectives from 315 pieces of sample from site A and 5 defectives from 315 pieces of sample from site B. Unfortunately, time was lost to catch up with the scheduled sales promotion.
My later analysis showed that the original defective was 5.5% combined (average 1% from site A and 10% from site B). The probability of this original lot passing the inspection is 25% (I will explain this in detail when we discuss OC Curve later). When the producer conducted the first screening of the lot, they reported that 2% defectives were found, which effectively reduced the overall defectives percentage from 5.5% to 3.5%, as 100% inspection is not considered an effective means to screen out all defectives. The probability of the first screened lot passing the second inspection increases from 25% to 85%.
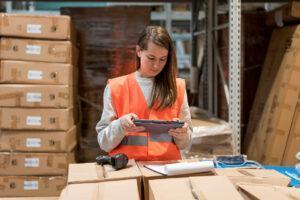
screening of the lot, they reported that 2% defectives were found, which effectively reduced the overall defectives percentage from 5.5% to 3.5%, as 100% inspection is not considered an effective means to screen out all defectives. The probability of the first screened lot passing the second inspection increases from 25% to 85%.
We were fortunate that this 30,000-piece lot got rejected; otherwise, we could have shipped the high defective lot from site B. Eventually, when the producer followed the instruction to separate the site A lot and site B lot, a significant percentage of defectives were screened and removed. As a result, both lots passed the inspection requirements and got shipped.
That was an important lesson learned. Manufacturing sites run by different teams with different assembly machines should be considered as producing different products, which warrants separate sampling inspection.
If lot formation had been considered that way, the site-A lot would have been very likely to pass the first inspection. In contrast, the site-B lot would have likely failed the first inspection with many defectives uncovered, which might have triggered a more effective action to screen and clean up the site-B lot. If it had all happened like that, we might be able to catch up with the scheduled sales promotion.
As a company, we now learn that the economics of inspection and the quality of the accepted product are greatly influenced by the manner of lot formation, as shown in the above example.
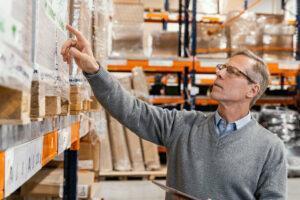
2. Lot-by-Lot Inspection
Before I delve into the more extensive subject of sampling inspection, I like to define some terms to facilitate our discussion later.
When a product is submitted in a series of lots (termed lot-by-lot), the acceptance sampling plans typically include the following terms and symbols:
N = lot size
n = sample size
c = acceptance number, i.e., the allowable number of defectives in the sample
r = rejection number ·
When more than one sample per lot is specified (e.g. double sampling), the successive sample sizes are designated as n1, n2, n3, etc. The successive acceptance numbers are c1, c2, c3, etc. The successive rejection numbers are r1, r2, r3 etc.
Single Sampling, Double Sampling, and Multiple Sampling
Our contract inspection company conducts single sampling in pre-shipment inspection. Under some particular circumstances, we may instruct the inspector to do a double sampling inspection, but never multiple sampling.
In single-sampling plans, the decision to accept (= or < c) or reject (= or > r) a lot is based on the results of the inspection of a single group of units (n) drawn from the lot (N).
In double-sampling plans, a smaller initial sample (n1) is usually drawn, and a decision to accept (= or < c1) or reject (= or > r1) is reached based on this smaller sample if the number of defectives is either quite large or quite small. A second sample (n2) is taken if the first results are not decisive. Since drawing and inspecting the second sample (n2) only in borderline cases is necessary, the average number of pieces inspected per lot is generally smaller sampling.
The multiple sampling plans in the ANSI/ASQ Z1.4 standard all provide for 7 samples. In all the AQL standards, all of the individual samples in any multiple sampling plan are of the same size. I will outline the following schematic operation of single, double, and multiple sampling.
Single sampling: This is adopted as a pre-shipment standard of “Quality First”, the company I work for, unless otherwise instructed.
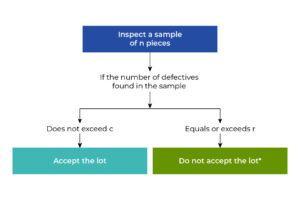
Double sampling: This is only adopted in a rare situation when conformance confidence is met by referencing reliable quality records, implemented only under Quality First special instruction. When double sampling is enacted, both samples are drawn at the same sampling time to simplify the required administration.
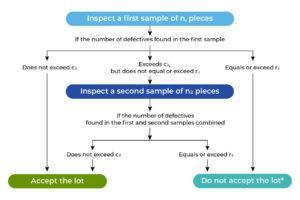
Multiple sampling: This is never enacted by Quality First for pre-shipment inspection.
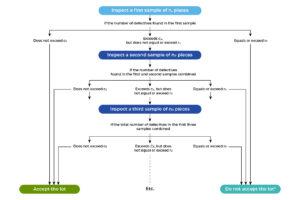
Using AQL tables of ANSI/ASQ Z1.4
Although using the sampling tables appears straightforward, I want to discuss a special situation where several uncommon rules are required. Such practice is hidden in some pre-shipment inspection reports I received.
Single sampling table of ANSI/ASQ Z1.4
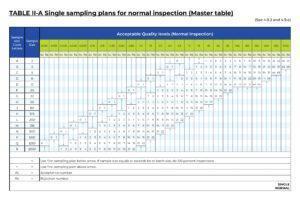
Sample size code letter table of General Inspection Levels of ANSI/ASQ Z 1.4
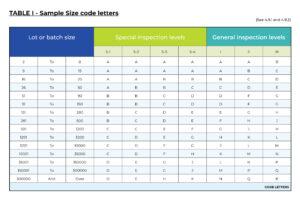
Our inspectors use the above two tables to determine the sample size for a lot identified and submitted for inspection. The following examples illustrate how that is done and what inspectors should be aware of:
Our policy specifies the following:
AQL 2.5% for major defectives
AQL 4.0% for minor defectives
General Level II
In using these two tables, for a lot size of 160,000, the first thing required to determine is the sample size code letter. For a lot size of 160,000 and General Inspection Level II, the Sample Size Code Letter Table gives the code letter as P. In the Single Sampling Table, it is found that the sample size for single sampling is 800.
But this table does not offer a plan for AQL 2.5%. Instead, the symbol of the upward pointing arrow directs the user to the sample code letter N, and the required plan is:
Sample size: 500
Acceptance number: 21
Rejection number: 22
Again, this table does not offer a plan for AQL 4.0%. Instead, the symbol of the upward pointing arrow directs the user to the sample code letter M, and the required plan is:
Sample size: 315
Acceptance number: 21
Rejection number: 22
We now have different sample size to inspect for major defects (500 pieces) and minor defects (315 pieces). We, therefore, require inspectors to inspect for both major and minor defectives in the first 315 pieces of sample. Subsequently, in the remaining 185 pieces of the sample, inspectors only include minor defectives in the lot acceptance decision despite major defectives found in these remaining 185 pieces. Any major defectives found from these remaining 185 pieces are reported only for information, not for lot acceptance determination.