Pre-shipment Inspection – Sampling Risks
by: Quest Claire
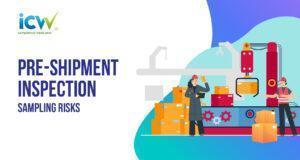
I briefly discussed sampling risks to buyers and producers in the previous sections. I also want our producer to be fully aware of and understand these risks, even though I feel comfortable about them. Those risks are a result of the following:
- The inherent nature of sampling
- Combining different products into a single inspection
- Splitting a large lot into multiple sub-lots for inspection
Risks due to the inherent nature of sampling
In any attempt to discuss the inherent nature of sampling, I must introduce an essential concept of Operating Characteristic Curve; in short, people call it OC Curve. It is a statistical tool I use to gauge if the sampling plans used in our pre-shipment inspections impose too much risk either to Quality First as a buyer (buyer’s risk) or to the vendors as producers to Quality First (producer’s risk). In addition, I am responsible for presenting and explaining such risks to our company management and vendors when necessary.
The concept of OC Curve
For attribute sampling plans, the OC Curve is a graph of lot fraction defectives, p versus the probability, Pa, that the sampling plan will accept the lot.
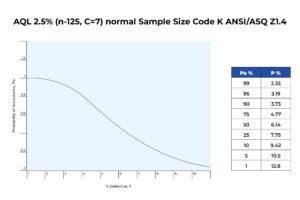
The above figure shows the curve of behavior that would be obtained if an inspector were instructed to take a sample of 125 pieces from a lot of 3,000 pieces and to accept the lot if no more than 7 defective pieces are found, based on Normal General Inspection Level II AQL 2.5%.
Therefore, a good lot with 2.33% defective (better than the requirement of 2.5%) has 1 chance in 100 of being rejected. As this is good quality, this is the inherent sampling risk to the producer despite the tiny chance of 1 in 100.
On the contrary, a bad lot with 6.14% defective (worse than the requirement of 2.5%) has 50 chances in 100 of being accepted, also called Indifference Quality Level. Moreover, a bad lot with 9.42% defective (much worse than the requirement of 2.5%) has 10 chances in 100 of being accepted. As this is bad quality, this is the inherent sampling risk which Quality First, the buyer must tolerate.
Currently, we inspect based on General Inspection Level II AQL 2.5% across the board for all the product categories we carry. I wonder if we should use a single Inspection Level for protection across the entire spectrum of product categories. I understand there are different risks of nonconformance from the product safety point of view, material variations and process variations from a quality control standpoint.
Additionally, based on my analysis of inspection reports for different product categories, I collected sufficient data to support that we should not use a single Inspection Level but rather a different Inspection Level to cope with these risks we discussed. In other words, a higher Inspection Level should be used to cover higher-risk products.
In my process improvement plan, I recommend that Quality First classifies products into 3 categories for pre-shipment inspection. Each category specifies a different Level of Inspection, respectively General Inspection Level I, II, and III, based on the product nonconformance severity, quality variation or product safety risk to our customer. The 3 categories are:
Level 1: classified as high-risk items which are subject to General Inspection Level III, they include toys, children’s products, electrical A/C product
Level 2: classified as medium-risk items which are subject to General Inspection Level II, they include wearing apparel, shoes, labor-intensive items
Level 3: classified as low-risk items which are subject to General Inspection Level I, they include kitchenware, decorative items, and houseware, which are all non-electrical A/C items
I want to discuss each of these three levels of inspection as follows, using a lot size of 3,000 pieces for a single normal inspection at AQL 2.5%.
Level 1: high-risk items
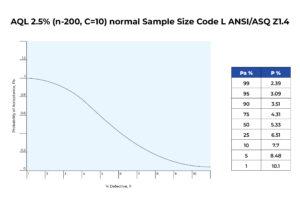
Level 2: medium-risk items
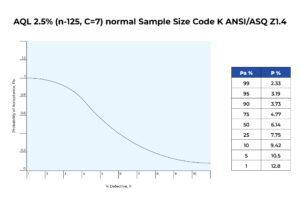
Level 3: low-risk items
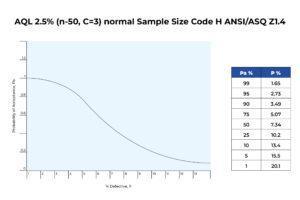
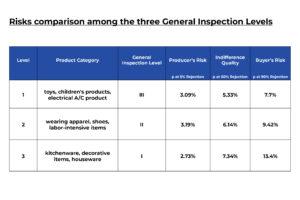
Observation and analysis:
- The producer risk ranges from 2.73% to 3.19% at 5% rejection. The range is relatively small, 0.46%.
- The buyer risk ranges from 7.7% to 13.4% at 90% rejection. The range is quite significant, 5.7%.
- The Indifference Quality Level ranges from 5.33% to 7.34%.
- Switching from General Inspection Level I to III slightly changes the producer’s risk but significantly reduces the buyer’s risk. Such switching is usually initiated by the buyer and accepted by the producer.
There are two OC Curves which I want to bring to everybody’s attention because they can be considered as building blocks in the overall concept of OC Curve. They help everybody visualize the OC curve’s shape change when the sample size, n changes or the acceptance number, c changes.
The first OC curve is n = 1, and c = 0, which means one piece of sample is drawn; if it is good, accept the lot; if it is bad, reject the lot.
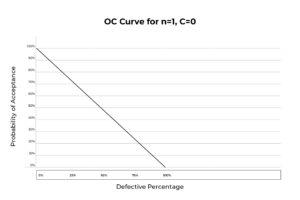
The second OC curve is on 100% inspection, which means all the pieces of the lot are drawn; if they are all good, accept the lot; if one piece or more is bad, reject the lot.
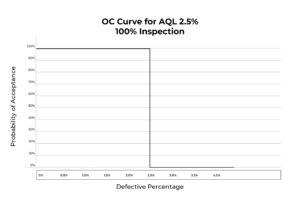
Along with the previous OC curves we reviewed and discussed, I would like to characterize the shapes of OC Curve as follows:
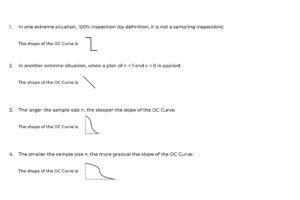
In summary, the larger the sample size n, the larger the acceptance number c, which gives the OC Curve higher discriminatory power. In other words, a higher discriminatory power sampling plan reduces the likelihood of making a bad sampling decision to accept a bad lot or reject a good lot.
Before leaving this OC Curve subject, I also want to state the importance of two additional concepts, which are important in selecting AQLs to protect buyers’ interests. They are the Limiting Quality, LQ, and the Average Outgoing Quality Limit, AOQL.
Limiting Quality, LQ
In the previous discussion, I discussed that we must accept a low probability of accepting lots with a higher percentage of defective; we call it buyer’s risk. In ANSI/ASQ Z1.4, LQ Tables of Pa 10% and Pa 5% are provided for reference and selection.
The LQ, once chosen, is the worst quality that the buyer is willing to accept. In our earlier example, we discussed LQ 10% for General Inspection Level III (7.7%), Level II (9.42%), and Level I (13.4%). Based on this information, the buyer can choose to conduct an inspection at which of these General Inspection Levels the company can tolerate.
The following table is designed for LQ 10%:
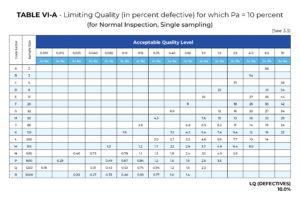
Average Outgoing Quality Limit, AOQL
There is an important assumption when ANSI/ASQ Z1.4 AOQL Tables were constructed. All rejected lots by the sampling scheme are 100% screened by the producer before resubmitting the lot for re-inspection. The AOQL represents the limit of the average quality of inspection lots which have been subjected to the sampling inspection, and each of which is accepted or rejected under the AQL plan applied.
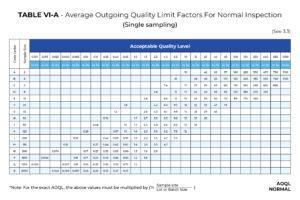
Combining different products into a single inspection
Combining different products into a single inspection is pretty tempting because of noticeable cost savings. As briefly discussed at the beginning of this article, products coming from two different production sites could be very different in quality; they should be considered different products for sampling.
There are many more questions: 1. should products of only different colors, 2. should garment of different sizes, or should ceramic cups of different graphic designs, … be considered as different products for sampling? When I have such a question, I review the possible sources of quality variation before different products are grouped as the “same” product for sampling purposes. Such a source of variation determination must be done systematically, using knowledge of production process equipment, materials, and people who run the production processes. If the review confirms no attributable variation is identified, different products are grouped to benefit from cost savings for inspection. If in doubt, I will have inspections done separately in the beginning until I get sufficient inspection data for review. In practice, we have instructed our contract inspection company to treat garment of different sizes, ceramic cups of different graphic designs, and plastic containers of different colors as “same” products for sampling purposes.
Splitting a large lot into multiple sub-lots for inspection
I want to use an actual example to discuss this critical topic. We had an important promotional activity a year ago. We started the promotion on September 1, using our anticipated bestseller, kitchenware. The total quantity of the best seller targeted to be sold was 12,000 pieces for 2 weeks. Production was scheduled to start on June 1 and complete on June 30; productivity was 2,000 pieces every 4 days.
We had two choices for pre-shipment inspection: (1) Inspected the total lot of 12,000 pieces on June 30, or (2) Inspected 6 sub-lots, every 2,000 pieces in every 4 days until we finished all the 6 pre-shipment inspections on June 30.
Potential Factors for Consideration in Making the Choice
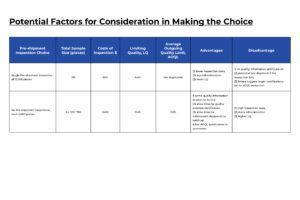
Conclusion:
Six pre-shipment inspections were chosen despite higher inspection costs and more administration work. Since the promotion window was locked up with other companies corresponding activities, the ramification from late shipment is much larger as there are intangible costs to bear. Because of such concern, the benefits of inspecting early on smaller lot protect the company from facing risks of losing any business, which must be taken into consideration in the total cost of quality.
Although all six pre-shipment inspections passed on their first submission to pre-shipment inspection, this decision is documented as one of the best practices the company will continue to follow.
Splitting a large lot into multiple sub-lots for inspection does not seem to be beneficial to Quality First without the promotion event consideration. Simply from an inspection costs standard point, it makes more sense to conduct one pre-shipment inspection, provided the producer has sufficient storage for the entire lot and can present it as a whole for random inspection.
Therefore, companies want to conduct an independent pros and cons study and determine how to inspect so that they can cover their interests and concerns.